Sevaan Group’s expertise in different types of welding

At Sevaan Group, our welding workshop is the perfect example of our smart factory at work… where our exceptional team of specialist welders work in unison with robotic welders. By combining skilled physical production with advanced digital technology, we provide you with the best solution for your product.
We perform intricate welding work while maintaining high productivity and precision accuracy. No matter the complexity of your welding task, we will complete the project to the highest standard.
We take a look at our expertise in different types of welding, including MIG welding, TIG welding, spot welding and robotic welding.
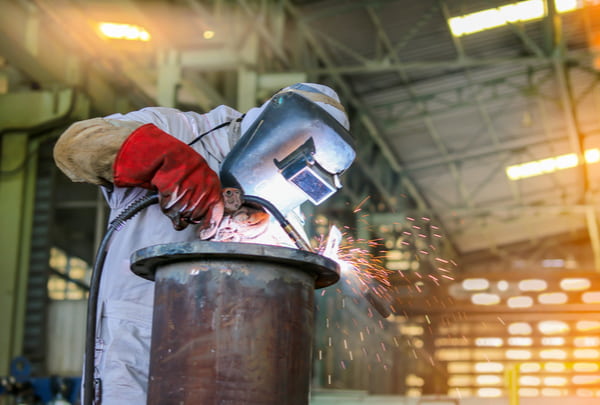
MIG welding
Metal Inert Gas (MIG) welding is an arc welding process that uses a continuous solid wire electrode heated and fed into the weld pool from a welding gun. The two base materials are melted together, forming a join.
The gun feeds a shielding gas alongside the electrode, helping protect the weld pool from airborne contaminants.
MIG welding is a versatile technique suitable for both thin sheet and thick section components.
MIG welding is widely used in most industry sectors and accounts for more than 50 percent of all weld metal deposited. MIG welding also has the advantage in terms of flexibility, deposition rates and suitability for mechanisation.
Other benefits of MIG welding include:
- Productivity – The time you can save by not having to change rods, brush the weld or chip away slag can approximately double your productivity.
- Reduced costs – The increased productivity also lowers your welding costs and allows you to get more tasks completed.
- Good quality – MIG welding uses shielding gas to protect the arc from the atmosphere. This results in a good clean weld, where you don’t have to remove any slag, and being able to use both hands on the MIG gun helps with your control. Also, the wire feed and voltage settings allow for increased versatility.
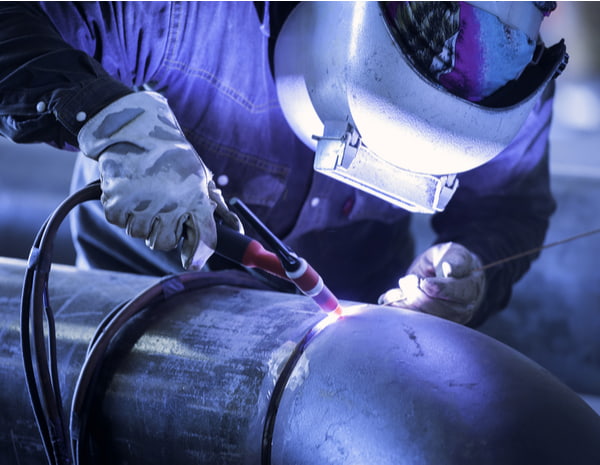
TIG welding
All welding requires the application of heat, which melts the metal being welded. With the TIG welding process, the heat comes from an electric arc that streams between the electrode in a hand-held torch and the metal being welded. The arc and molten metal are shielded by an inert gas, which protects the electrode and base metal from oxidising.
The most important skill needed for TIG welding is moving the torch in a controlled manner, with steady forward movement, while keeping the gap between the tip of the electrode and the base metal consistently small.
It requires a lot of practice to precisely control the arc length, keeping it as short as you can without allowing the electrode to touch the base metal or filler rod.
TIG welding has a range of benefits, including:
- Welds more metals and alloys than any other process – TIG welders can be used to weld steel, stainless steel, chromoly, aluminium, nickel alloys, magnesium, copper, brass, bronze and even gold.
- Creates high quality, clean welds – With superior arc and weld puddle control, TIG allows you to create clean welds when appearances count.
- No sparks or spatter – Because only the necessary amount of filler metal is added to the welding puddle, no spatter or sparks are produced.
- No smoke or fumes – TIG welding does not create smoke or fumes, unless the base metal being welded contains contaminants or elements such as, oil, grease, paint, lead or zinc.
- Welds in all positions – TIG welds can be made in all positions – flat, horizontal, vertical or overhead.

Spot welding
Also known as resistance spot welding, spot welding is a welding process that involves the use of an electrical current to join two or more metal surfaces. It’s typically used to join sheet metal.
As the respective metal surfaces heat up, they fuse together from the heat created by the electrodes.
Spot welding requires the use of copper alloy electrodes to focus an electrical current into a small area between the metal surfaces to be joined.
The electrodes are also designed to create pressure, which is responsible for holding the workpieces in place. As the copper alloy electrodes create heat, the metal workpieces fuse together in a controlled manner.
Spot welding offers several advantages, one of which is the ability to harden the workpieces. Because it uses heat to melt and fuse the surfaces of metal workpieces, it tends to make them harder.
Spot welding is also a fast welding process. Like with other welding processes, the weld time varies depending on the thickness of the workpieces. Thicker workpieces tend to have a longer weld time than thinner workpieces.
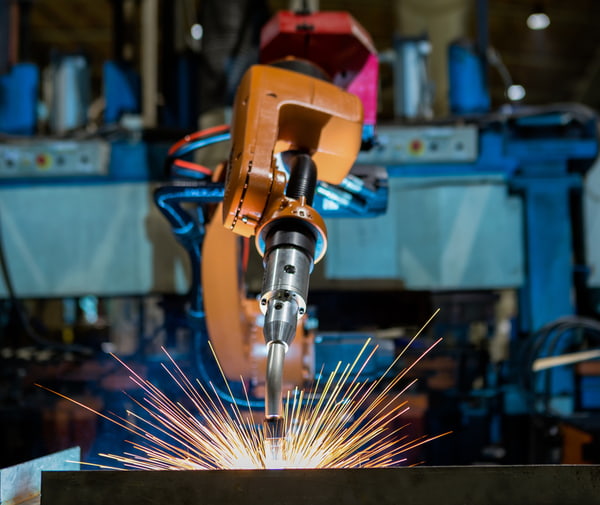
Robotic welding
Robotic welding, also called automated welding, is the automated process of using mechanised programmable tools to weld and handle a part. A robot welding unit, also called a robot welding cell, consists of several components working together to weld pieces. These components include those actively taking part in the welding, as well as accessories and safety features to ensure the smooth operation of the cell.
Programs are input and saved to the controller, which tells the robot what to do. These programs move the welding robot and manipulate the torch on the end of its arm, placing it exactly where it needs to be at any point.
The torch heats up, using a power supply to generate enough heat in the metal to fuse parts together permanently. The wire feeder feeds extra material to the robot arm to do this. Between parts, the arm moves the torch to the wire cleaner to remove any spatter.
While a robotic welding system often calls for a hefty upfront investment, it can also improve bottom-line business performance from the first day of operation. Some benefits include:
- More consistent, higher quality welds
- Greater productivity, yields and throughput
- Reduced waste and less rework in general
- Drastically reduced post-weld clean up.
At Sevaan Group, we’re confident that leaning into new-generation technology gives us the capability of transforming operations and outcomes. Our facility combines high tech machinery with formidable manpower to provide excellent outcomes for all our clients.
If you have a new project in development, contact our exceptional team of metalwork technicians… and together we can discover new robotic opportunities.